While being phased-out from firefighting systems, per- and polyfluoroalkyl substances (PFAS) are found in aqueous firefighting foams (AFFF) and equipment. Helping the industry cope with this challenge, TRS Group is optimizing a method for cleaning PFAS out of fire extinguishing equipment. Below we discuss the challenges of AFFF removal and have a discussion of an effective solution.
How is PFAS different than other contaminants?
With the fluorine-containing tails (shown to the right in green) and different functional groups (heads shown in red), PFAS molecules are stable chemically and physically and are quite different to treat than solvents and
petroleum hydrocarbons. Unique PFAS characteristics include:
- The heads may be neutral, cationic, anionic or zwitter-ionic.
- The molecules can act as bases and acids.
- The remediation goals are often in the nanogram per liter (ng/L) range, orders of magnitude lower than the typical concentration goals for solvents.
- The molecules have an affinity for air-water interfaces. In elevated concentrations, they may form foams due to their surfactant properties.
These properties create challenges for remediation and PFAS cleanout, with a need to keep the chemistry in mind when selecting methods.
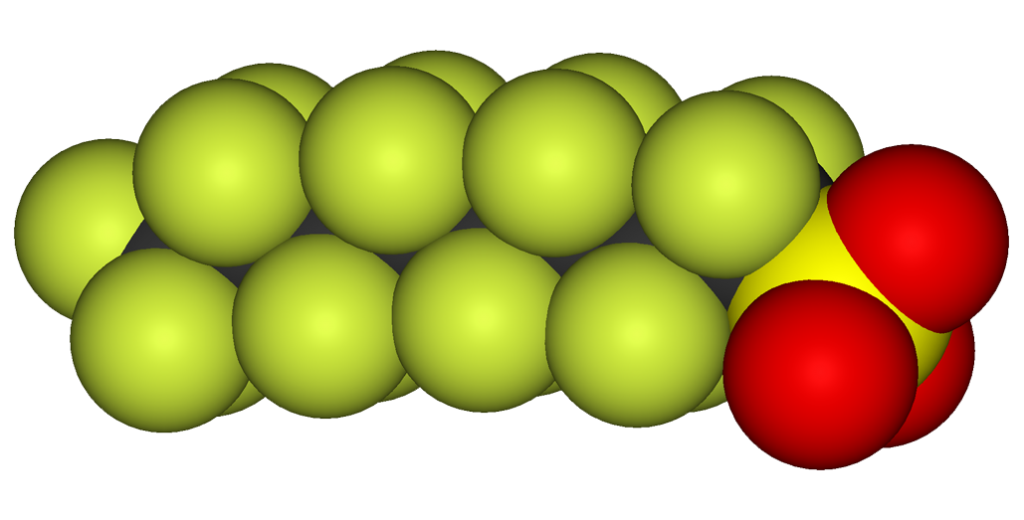
Taking PFAS out of solution
Although PFAS can be removed from water using ion exchange and granular activated carbon (GAC), due to their low affinity for GAC and low dissolved concentration goals, the frequent replacement of GAC and regeneration of resins lead to high operational costs. The industry is working intensely to find lower cost PFAS water
treatment solutions.
One such solution is called the PerfluorAdTM method. Once dissolved in warm water, this sustainable food-grade and honey-like product binds the PFAS molecules to form tiny flocs, which are clusters of PFAS and oleic acid particles. The floc is heavier that water, which we can remove by a combination of settling and filtration.
Cleaning agents that facilitate desorption and dissolution and then bind the PFAS will be more effective than traditional surfactants and solvents.
Removing AFFF from fire-fighting equipment
AFFF typically contains 3 to 10 percent (%) PFAS by weight. The remaining fluids are carrier liquids, such as glycols, esters and polyglycocides in varying formulations. In a standard 30-gallon foam tank, the PFAS mass is 5 to 10 kilograms (kg). Unfortunately, triple-rinsing (or more) with water has not been as effective as desired.
The majority of the PFAS is removed by draining the AFFF from the systems, as illustrated to the left below.
While fresh AFFF concentrate is liquid and readily transferred to foam tanks aboard the vehicles, over time AFFF may become viscous, form solid coatings, and attach
itself to tank surfaces and pipes. Such PFAS-rich crust build-ups are challenging to remove, unless the surfaces are accessible and can be cleaned by scraping and pressure washing. Crusty build-up removal is facilitated by physical agitation.
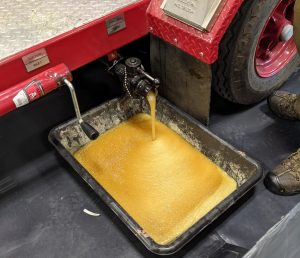
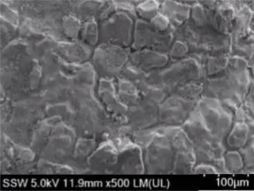
Since most of the internal surfaces are inaccessible, it is crucial that the cleaning method and agents work well in the nooks and crannies of the tanks and piping. Agents, such as PerfluorAd, ensure that crusts and liquid AFFF residues are dissolved, as the chemical flocculation pulls PFAS away from the deposits.
The most cost-efficient rinsing involves heated surfactant-like agents and physical agitation. This is particularly true for vehicles that have been in service for a long time and have substantial residues of older foam concentrate or crusty deposits.
Minimizing waste generation
The PerfluorAdTM cleaning process uses between 500 and 2000 gallons of water for each truck. We first flush potable water through the truck. Thereafter, we heat the water and add PerfluorAd. Notice the crud in the bottom left photo below. Clearly, adding PerfluorAd has a significant impact on AFFF removal.
We remove the majority of the PFAS as a small amount of flocculant in the
cone-bottom tank shown below in the large photo. The waste stream generated is a few gallons of sludge.
A significant feature of the PerfluorAdTM process, is we treat the rinsate, further
reducing the generated waste, which results in substantial cost savings. Lastly, we polish the water in granular activated carbon (GAC) vessels prior to discharge.
Future improvements to the system may include destructive water treatment
processes, such as sub- or supercritical water oxidation to further reduce the amount of waste produced.
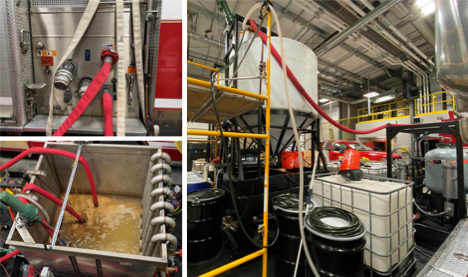
Rebound
At the end of the AFFF removal, we flush the foam tanks and the piping system repeatedly with clean water. Once we reach non-foaming conditions, we sample the water for analysis. We typically achieve reductions in PFAS concentration by more than 99.8%. Our calculation shows that where a typical fire extinguishing event would lead to the release of 5 to 10 kg of PFAS per un-cleaned truck, a similar event after cleaning with PerfluorAd would release about 10 to 20 milligrams, a reduction by 99.9998%. That said, the resulting water is not clean enough to drink.
As PFAS adsorbs and diffuses into solid surfaces, some are concerned that testing months later would show that PFAS concentrations in the tanks have rebounded; that is, have back diffused out of the impacted surfaces. This would occur if significant PFAS mass diffused or dissolved out of pipes, fittings or hoses over time.
A useful testing method would be to repeat the final rinse and sample the water again sometime later. A better approach would be to hook up to a fire hydrant and simulate a real fire event by running water and fluorine-free foam through the vehicle into a large tank where samples can be collected. We note the importance of using the same spraying force as during a real event. Other real-world testing could include using the truck’s engine to engage a power take-off (PTO) to run pumps that pressurize the firefighting water. A reasonable conclusion is that any PFAS that diffused out of the impacted equipment likely would not be measurable.