The United States Army Corps of Engineers (USACE), Omaha District, on behalf of the United States Air Force (USAF), selected HydroGeoLogic Inc. (HGL) and TRS Group, Inc. (TRS) to perform the final groundwater remedy at the Brandywine Superfund Site (Site) located on USAF Joint Base Andrews offsite property in Brandywine, Maryland. The remedy was completed under a performance-based contract and consisted of Electrical Resistance Heating (ERH) remediation of the groundwater plume source.
Initially, the Site was used by the United States Navy as a storage area from 1943 through 1961 (URS, 2006). From 1961 to 1987, the Site was operated by the USAF as a storage area for waste and excess government material (IT Corporation, 1999) generated by the United States Department of Defense (DoD) operations at various facilities, including Andrews Air Force Base (AFB), Bolling AFB, the Washington Navy Yard, the Naval Ordnance Station-Indian Head, and White Oak Laboratory (Dames & Moore, 1992). According to USAF records, hazardous materials and wastes, including spent solvents, were stored at the Site within drums and several concrete bins (Dames & Moore, 1991). Detailed information on where solvent drums were stored and how the wastes were handled at the Site is not available.
The contaminants of concern are chlorinated volatile organic compounds (CVOCs), primarily trichloroethylene (TCE) and 1,4-dichlorobenzene (DCB). Following 4 ½ years of groundwater pump and treat and three injection rounds of substrates for enhanced reductive dechlorination (ERD), the groundwater plume was reduced from 20 to 1.5 acres, representing more than a 90% area reduction. High resolution site characterization (HRSC) using membrane interface probe and passive flux meters identified a low permeability clay unit that was about 30 feet below ground surface (ft bgs) as the continuing source of contamination and rebound. The results of the HRSC indicated a limited residual source mass estimated at 300 pounds. The ERH remedial objective was to reduce TCE and DCB groundwater concentrations to a maximum of 5 micrograms per liter (µg/l) and 75 µg/l, respectively.
During ERH, an electrical current is passed through the soil and groundwater resulting in the TCE and DCB removal. As electrical power is applied to the treatment volume, the soil’s natural resistance to the flow of electrical current creates heat, which converts the liquid and sorbed phase CVOCs to the vapor phase. Further, the temperature of the soil and groundwater eventually reaches the boiling point of water, which converts the groundwater and soil moisture to steam, which acts as a carrier gas for the volatilized contaminants. The vapor recovery (VR) system collects the steam and target contaminants in the vadose zone for subsequent treatment by the above-grade vapor treatment equipment.
The 49,000 cubic yard ERH treatment volume was beneath and divided by a public roadway, a water and sewer main, private and government land, and two active CSX Transportation, Inc. (CSX) railroad tracks. These site features added significant complexity to the ERH system design and construction. Consequently, implementation of the remedy included coordination with many stakeholders, including the following:
- USAF
- CSX
- United States Environmental Protection Agency, Region 3
- Maryland Department of the Environment
- Prince George’s County Department of Health
- Prince George’s County Department of Permitting, Inspections and Enforcement
- Washington Sanitary Sewer Commission
- Private landowners
In order to apply ERH to the full treatment volume, installation of ERH electrodes between two active CSX railroad tracks and within the CSX right-of-way was essential. During system installation, on-site CSX oversight and rail watch was mandatory to avoid disruption of rail service and to maintain site worker safety. Since the railroad tracks are active, the placement of ERH electrode power cables and VR conveyance piping on or near the tracks was not an option. Therefore, cable and conveyance piping were placed under the railroad tracks, using jack-and-bore conduits, to not disrupt rail service or the integrity of the tracks. Four, 6-inch steel pipes were installed under the CSX railroad tracks and used as conduits, making necessary connections between the primary utility power service and the ERH equipment compounds and portions of the ERH treatment area between the tracks.
Due to the location of the CSX railroad tracks, TRS designed two ERH equipment compounds with two distinct treatment areas east and west of the tracks.
Additionally, TRS incorporated real-time elevation monitoring of the two active railroad tracks during ERH system construction and operations. TRS used an Automated Motorized Total Station (AMTS) system, which used a laser to measure movement of over a hundred mirror survey prisms mounted to the steel rail of the tracks. Prior to operations, TRS and HGL collaborated with key stakeholder, CSX, and identified various track deformation response levels and associated action. The first action, notification and inspection was required after reaching a 0.75 inch change in track elevation. The last and most extreme potential action included shutting the ERH system down if an elevation change of 1.5 inches was detected. This response level contained a safety factor of 0.5 inch to the Federal Track Safety Standards, 49 CFR Part 213.
Subsurface construction of the ERH system began in July 2018. The ERH system incorporated 43 vertical bored ERH electrode pairs and 58 sheet pile electrodes across the treatment area. Vertically bored electrodes were used in areas where stakeholder or utility clearance did not allow for the installation of sheet piles. In these areas, a vertical bored electrode pair was substituted for a sheet pile electrode. Additionally, a vapor recovery (VR) plenum was installed over the ERH treatment area. Seventeen (17) temperature monitoring points (TMPs) and eight compliance groundwater monitoring wells were installed to monitor ERH performance.
ERH system operations began on April 9, 2019. The system operated for 214 days and applied 7,435,773 kilowatt hours (kWh) of energy into the treatment volume. The VR and treatment system were operational for 214 days and removed approximately 1,716 pounds of volatile organic compounds (VOCs). On average, subsurface temperatures within the treatment volume increased at a rate of approximately 1.4 degrees Celsius (°C) per day, as the temperature increased from ambient to boiling temperatures.
During operations, TRS provided CSX weekly monitoring updates. Track elevation changes, continuously recorded by the AMTS system, were below the lowest response limits approved by CSX.
During ERH system operation, HGL collected groundwater samples from nine groundwater monitoring well locations within the ERH treatment area. The first round of confirmation groundwater samples was collected on June 4, 2019. The last round took place on November 5, 2019. Due to the tight clay formations within the ERH treatment volume, the recharge of groundwater to several of the groundwater monitoring wells was slow to near non-existent during electrical energy application. During the 214 days of ERH system operation, power application was interrupted for a total of 31 days to allow for groundwater recharge into the ERH treatment volume.
To accommodate groundwater recharge, power application to the treatment volume ceased on October 31, 2019. The results of the November 5, 2020 confirmation groundwater sampling event concluded groundwater samples collected from all groundwater monitoring wells met the treatment goals of 5 µg/l TCE and 75 µg/l DCB, with the exception of groundwater monitoring well DP61 at 5.68 µg/l of TCE. Demobilization activities of the ERH system commenced shortly thereafter and concluded on December 31, 2019. On December 31, 2019, the USAF and private property owner reviewed Site conditions and agreed that TRS and HGL had satisfactorily completed restoration activities. Additionally, TRS met with CSX on January 6, 2020 for a final inspection.
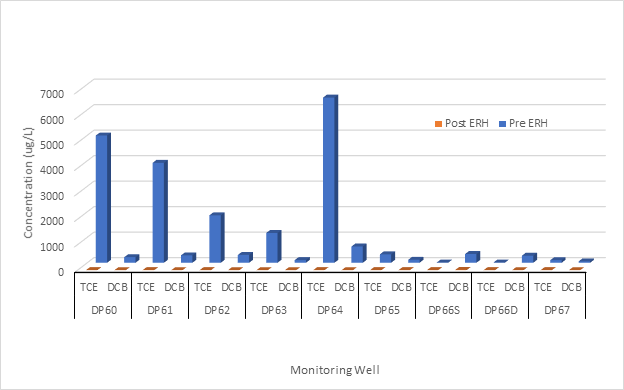