Matt Pockette discusses his role as a Corporate Safety Manager & his efforts to maintain workplace safety.
Position: Corporate Safety Manager
Location: Indiana, IN
TRS Employee Year Started: 2024
Certifications: Electrical Safety Compliance Professional (CESCP) Certified, 40-hour HAZWOPER Certified, Eight-Hour HAZWOPER Supervisor Certified, OSHA Construction Certified, OSHA General Industry Certified, CPR, First Aid and AED Certified & Certified Instructor, Safety Auditor Certified, EM-385 40-hour Certified.
TRS: Can you tell us a bit about your background and how you became our Corporate Safety Manager.
Matt: I spent 21 years in the US Air Force as a Loadmaster on the C-130 and an In-flight refueler on the KC-135. While I spent most of my time flying and deploying around the world, I managed multiple safety and training departments. I also attended a variety of safety courses and schools throughout my career and enjoyed that expanded duty. When I retired from the military, I took a position with a waste and recycle company as a Safety Supervisor.
While I really enjoyed the job, I was seeking a higher-level management position, one that could help to have more of an impact on day-to-day safety on-site. I saw TRS was hiring for a Safety Manager and the job description seemed to be exactly what I was looking for. I applied and after a few interviews here we are.
TRS: Why do you believe safety is so important within the workplace, specifically in our industry?
Matt: In our line of work, environmental hazards can leave an employee with lifelong health issues. A commitment to safety protects employees from injuries, illnesses and fatalities, creating a secure environment. Implementing safety protocols helps to prevent accidents and long-term health issues.
TRS: What are some common safety hazards in our industry and how do you address them?
Matt: Some common safety hazards are Electrical, Chemical, and Slips, Trips and Falls.
We have a very robust training program that not only teaches our field staff how to identify hazards but also how to mitigate hazards.
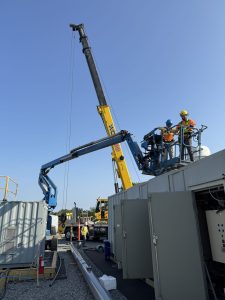
TRS: Please share some of the safety initiatives you have implemented or continue to encourage.
Matt:
- Regular Safety Training Sessions
- Hazard Identification and Reporting Programs – Encouraging employees to actively participate in hazard identification and reporting fosters a collaborative safety culture. Establishing a user-friendly reporting system empowers employees to promptly report unsafe conditions, enabling swift corrective action and prevention of accidents.
- Personal Protective Equipment (PPE) Programs.
- Open Communication Channels – Promoting safety in the workplace thrives on open communication. Encouraging employees to voice their safety concerns, suggestions, and observations establishes a culture of transparency.
TRS: How do you stay updated on the latest safety regulations and practices?
Matt: Continuing education. I take courses, read the latest regulations and develop training courses to not only grow professionally but also to make sure our employees are getting the most up to date information.
TRS: What do you enjoy most about working with TRS?
Matt: The people. I really enjoy getting to know each person, talking with them on project sites or virtually.