Greg Knight recently spoke about his new role at TRS as PerfluorAd Operations Manager and his role in implementing the AFFF removal technology.
Position: PerfluorAd Operations Manager
Location: Denver, Colorado
TRS Employee-Owner Year Started: 2004
Specialties: Electrical resistance heating (ERH), industrial wastewater, document review
Education and Training: Central Michigan University
TRS Group: What is your role in implementing the PerfluorAd® technology?
Greg Knight: As with any typical project manager role, it’s all about managing your resources. But I was thinking about this, and the thing we’re really trying to do is apply the technology to get the best results and to keep refining that process, always looking for ways to improve.
One of the things that we’re trying to do with PerfluorAd is to minimize the amount of waste generated. I look at it as my primary job to figure out how we can reduce waste, make the process more efficient, minimize offsite disposal and reduce costs.
TRS: What progress have you made improving the PerfluorAd process?
Greg: We are currently focused on speeding up the process. When we built our first system, it was kind of low-key, very portable, very simple. You know, keep it simple, stupid concept. It works well but it could be better. So, refining some of the processes like looking at the different pumps that we’re using and some of the different ways to approach a fire truck when you clean it.
That was one of the biggest surprises going in to our first job. No two fire trucks are alike, even similar makes and models. There are quite a few differences in how they operate. We learned a lot in a really short amount of time and I’m sure we’re going to learn more going forward, but I think we’ve made some good strides in improving our batch system.
TRS: What have you learned about minimizing the produced waste?
Greg: We are learning along the way – some the hard way; some through osmosis. When we started the Connecticut project, we were generating more waste than we wanted. I was talking to Steve Pistoll, our field technician, and to Cornelsen, the company that developed the technology, and realized we had a window of time to reduce that waste, so we changed our process a bit at about the midway point of that first phase. We were successful and able to minimize the waste generated, which was a good thing. We are working on taking our approach to the next level.
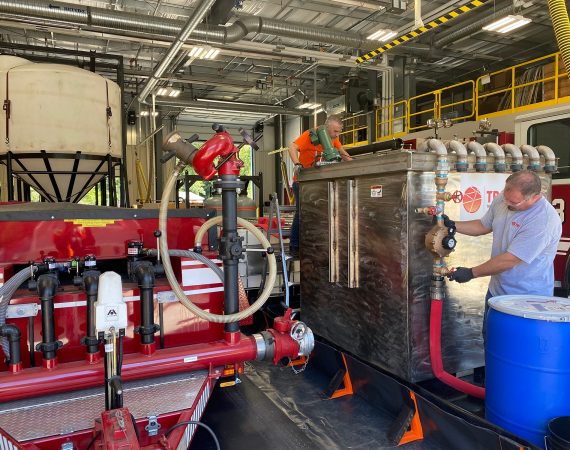
TRS: How has your role at TRS changed?
Greg: You could write a book about this alone. I got hired as an assistant project manager doing ERH projects. That was very short-lived, as I moved up to project manager. I did that for a few years and then moved up to senior project manager for the West Coast region. I did that for a few years. Then an opportunity came up when the QSAT (Quality, Safety, Assets, and Training) group was being formed and I took it.
With an eye for detail, it was a good choice to try to get consistency across the company; to try to use the same materials, the documents look the same from region to region; the output to the clients all look the same. So that was my goal.
We had a safety guy who left the company, so I took over the role, too. And that turned into five years of mostly safety and some quality. And then this came up with PerfluorAd, which was intriguing to me having a wastewater background.
TRS: Did someone come to you with this opportunity, or did you volunteer for it since you had the wastewater background?
Greg: It was kind of both. It has been a good fit.
TRS: What single thing have you been most proud of during your time at TRS?
Greg: I firmly believe that all the good things that happen at TRS happen because of teamwork. TRS is built on the team aspect.
I’m a firm believer that at TRS the sum is greater than the parts.
During my Quality Manager days, I was involved in helping improve performance consistency. But I didn’t do anything by myself. It took teamwork.
If anything, I feel like I contributed to that culture where quality and the finished product is very important.
TRS: What is the most satisfying aspect of your job?
Greg: The variety and the lack of repetition. Every project is different.
Also, there is closure. When we complete a project, almost always there is no further action. That is very satisfying.
That kind of ties back to the previous question in that the camaraderie and teamwork is the thing that’s kept me here. It’s just a great group of people.
TRS: What attracted you to the environmental remediation field?
Greg: I was a victim of opportunity.
I met my wife in Michigan and she wanted to move back to Denver. She’s a Denver native. And there was nothing for us in Michigan that was really holding us back. So, we moved and I found a job right away but it was kind of a factory job. And then my wife’s coworker’s husband said he was looking for someone to run their equipment warehouse. I knew I could do it, and one thing led to another and they hired me. It was an environmental firm, Parsons. They’re a big consultant. It was this corporate world, and in the Denver office they needed a new equipment manager.
Basically, I was taking care of a fleet of vehicles and field and sampling equipment for groundwater remediation and soil sampling and some other things that they did.
Parsons got me trained up and all of a sudden I was in the field doing groundwater sampling. It just kept escalating. Eventually, TRS was a subcontractor to Parsons at a project in Denver. I reached out to them two years later and sure enough they had an opening and here I am.