Our FlexHeater elements for implementation on thermal conduction heating (TCH) sites use less metal than competing technologies, do not require fossil fuel, and are recycled from project to project. In fact, our elements use roughly a quarter the amount of alloys of our competitors.
By Gorm Heron, Emily Crownover, Dan Oberle and Chad Crownover
Improve or fade away
At TRS Group (TRS) our goal is to seek improvement in everything we do. Each day we want to be a bit better than the previous day. Year to year we want to become more efficient, use less energy, and reduce the cost of our thermal remediation solutions. This push towards efficiency is lowering our treatment costs and making our solutions more sustainable.
Of course money matters; sustainability does too
We believe as time goes on there will be a greater emphasis on sustainability, which will influence remedy selections. We will see more energy-intensive services and activities leading to resource depletion incur taxes or fees. By focusing on our current environmental impacts (i.e., climate, resources, toxicity) we are preparing ourselves not only for overall improvement, but also for long-term cost-effectiveness. Efforts to reduce environmental impacts will translate into ways to reduce costs.
Thermal remediation has a huge footprint, doesn’t it?
We do use a lot of energy and hardware to heat the source zones and to treat the extracted fluids. The question is not whether in situ thermal remediation (ISTR) has a higher impact than doing nothing or doing a little (e.g., monitored natural attenuation (MNA), soil vapor extraction (SVE), pump and treat), it is how thermal treatment compares with the alternatives of similar effectiveness (Ding et al 2019). In this regard, thermal stands on its own, with the only other comparable remedy being excavation. This is particularly true for fire-training areas with elevated concentrations of per- and polyfluoroalkyl substances (PFAS), a very recalcitrant set of contaminants.
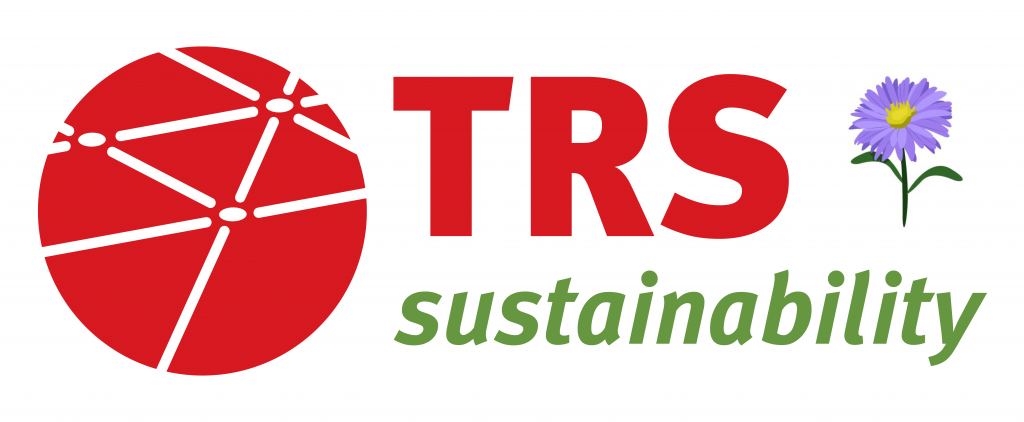
ISTR is more sustainable than excavation
Thermal compares favorably to excavation because:
- Excavation is avoided, reducing impacts to active facilities.
- Transportation to a treatment facility is avoided.
- Thermal treatment in situ or on site occurs at lower temperature than off-site thermal destruction, uses less energy, and reduces potential exposure and release pathways.
As a result, in-situ treatment of volumes over 2 to 3,000 cubic yards is more sustainable and usually less expensive than excavation (Crownover and Oberle 2020).
Thermal is often more sustainable than SVE
Thermal treatment is intense but efficiently solves the problem in less than a year. Hiester et al. (2003) showed that thermal treatment has a lower environmental impact than SVE, if the latter is expected to operate more than five years to accomplish complete removal of the source, which rarely happens. As a result, thermal treatment is usually more sustainable than SVE over the lifetime of the project.
How we are reducing our environmental footprint
Lemming et al. (2013) analyzed the life-cycle environmental impact of in-situ thermal technologies and identified the major impacts. The activities identified as having the largest impacts include:
- Energy usage
- Use of cement in grout seals and vapor covers
- Use of metals in heaters, electrodes, wells and equipment
- Use of activated charcoal for vapor and water treatment
TRS has active programs to improve our efficiency in each category. Table 1 provides a snapshot of those activities and intended impacts.
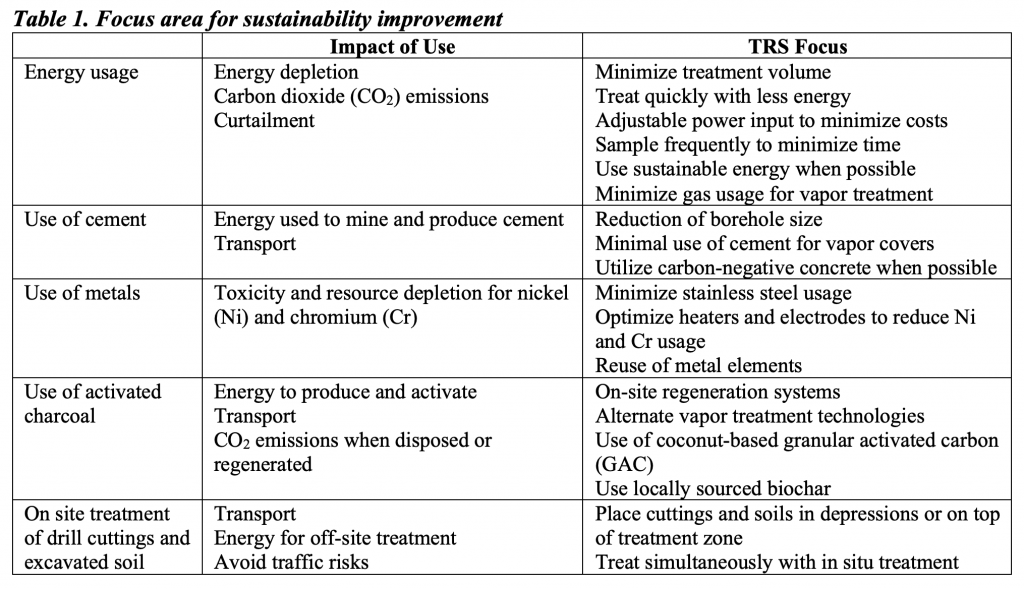
Additional options for improvement are summarized in Table 2.
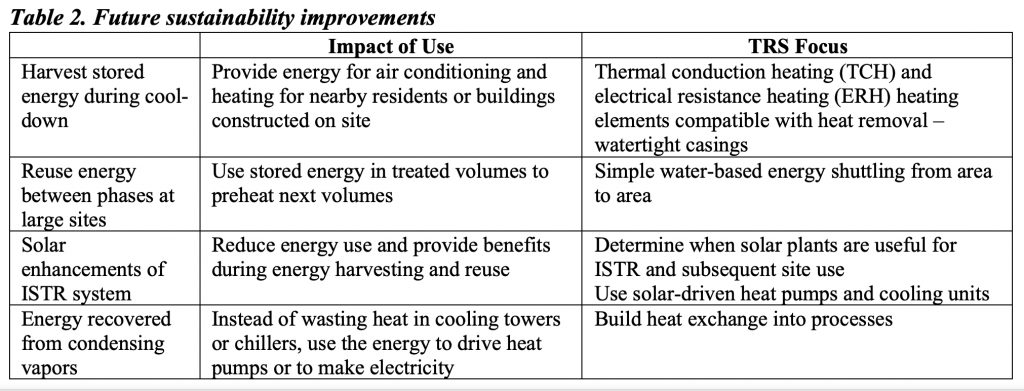
As a virtual company we have a head start
By having home offices throughout the country, which helps to reduce our travel, TRS uses less fuel and energy than competitors. Our ongoing optimization efforts are lowering our carbon footprint, reducing costs and saving our clients’ money. The additional optimization we do on the sustainable use of energy and material resources will make a similar impact as markets change to focus on sustainability.
References
Crownover, Oberle, D. (2020). Electrical resistance heating as a sustainable remediation technique. White Paper, TRS Group.
Ding, D., X. Song, C. Wei and J. LaChance (2019). A review on the sustainability of thermal treatment for contaminated soils. Environmental Pollution 253, 449-463.
Hiester, W., V. Schrenk, T. Weiss (2003). Environmental balancing of “cold” SVE and thermally enhanced soil vapor extraction – practical support for decision makers. Paper presented at ConSoil Conference, 2003.
Lemming, G., S.G. Nielsen, K. Weber, G. Heron, R.S. Baker, J.A. Falkenberg, M. Terkelsen, C.B. Jensen and P.L. Bjerg (2013). “Optimizing the Environmental Performance of In Situ Thermal Remediation Technologies Using Life Cycle Assessment”. Groundwater Monitoring & Remediation, 6 May 2013.